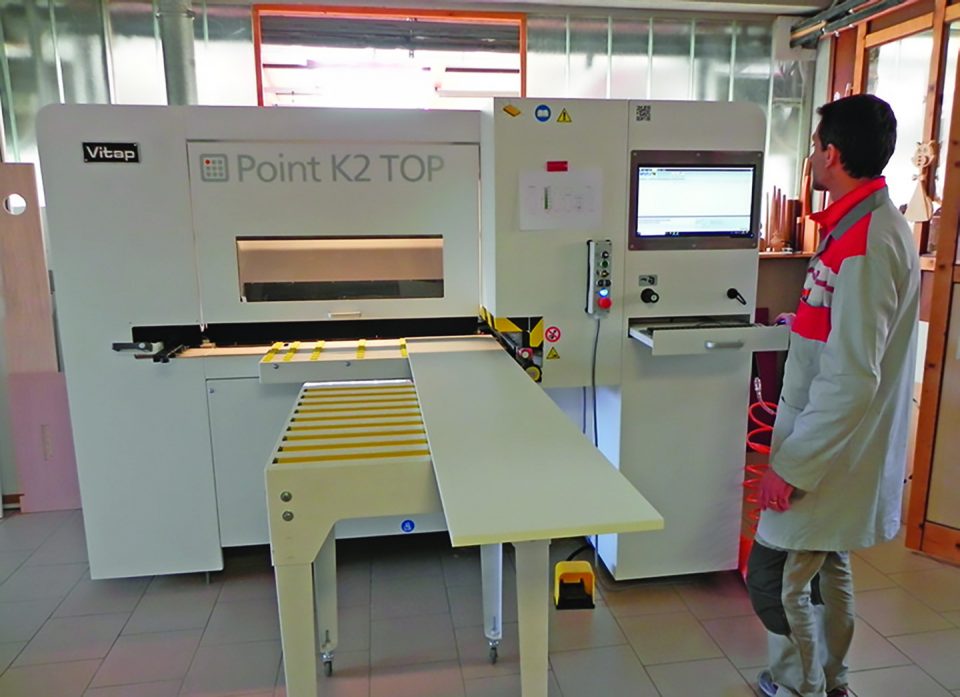
Liberi di inventare: come Point K2 Top ha risposto alle esigenze fondamentali di una falegnameria
La rivista Xylon, nel mese di aprile, ha dato voce alla falegnameria Papa, una sorprendente micro realtĂ che fa del pensiero creativo il proprio tratto distintivo e vincente da tre generazioni. Hanno raccontato come, introdurre il nostro centro di lavoro CNC Point K2 Top in azienda, sia stata una vera e propria rivoluzione copernicana per la loro realtĂ
Di seguito un estratto dell’articolo presente nel numero di maggio-giugno della rivista.
Alberto Papa e suo padre Enrico sono titolari di PapaArreda, un’azienda a conduzione familiare che si trova a Mergozzo, nella provincia del Vebano-Cusio-Ossola, che realizza mobili di altissima qualità . La PapaArreda rappresenta il dna artigianale ed è caratterizzata da quello che potremmo definire il “tratto somatico” dell’ingegno italiano; ha attraversato sessant’anni di storia e si riafferma, oggi, come espressione di una falegnameria d’eccellenza, in una reinterpretazione delle lavorazioni che ha scelto e integrato positivamente la tecnologia all’avanguardia della macchina per la lavorazione dei pannelli “K2 Top” di Vitap.
L’azienda opera in Lombardia, in Piemonte e in Svizzera. Gli “strumenti di marketing” privilegiati sono il passaparola – e questo la dice lunga sull’alta qualità del prodotto e del servizio – e il sito che descrive l’azienda in modo efficace, facendo leva sulla sua capacità di “customizzare”.
 UNA STORIA, UNA FAMIGLIA, UN’IMPRESA
Alberto Papa racconta quasi con ritrosia l’affascinante storia della sua famiglia, a partire dal nonno scultore, una professione d’artista, fortemente ancorata alla realtà territoriale: le cave di Candoglia, nel comune di Mergozzo, hanno “dato” il marmo per edificare il Duomo milanese.
“Mio nonno, Romeo Papa, ha cominciato, facendo lo scultore. Aveva frequentato la scuola di scultura e intaglio, negli anni Cinquanta e poi era “andato a bottega, come si diceva a quei tempi, da una scultore abbastanza affermato in zona, Germano Tedesco, per imparare il mestiere. A formazione completata, nonno Romeo ha scelto di separarsi dal maestro, avviando una attività tutta sua, ovvero la realizzazione di cornici per gli specchi in stile barocco. Torino era il suo mercato di riferimento, dove era piuttosto noto per la sua attività di subfornitore di elementi in marmo per arredatori e mobilieri”.
“Il nonno insegnava anche nella scuola ex Bellini, a Mergozzo, che formava meccanici e scalpellini del sasso. Mio padre inizialmente condivise la scelta del nonno, preferendo poi concentrarsi sulla lavorazione del legno, un’attività che appartiene alla tradizione territoriale, anche se oggi, le aziende locali sono più concentrate sul serramento. La specializzazione sull’arredo è andata calando, ma noi siamo rimasti legati al mobile, una vera e propria passione”.
Il passaggio dal marmo al legno
“Molti falegnami chiedevano fregi e lavorazioni in marmo per integrare la propria produzione di mobili, credenze e specchiere. La contaminazione di competenze e di“mestiere” è stata spontanea. Con il mio ingresso in azienda l’orientamento verso le opere da falegname è diventato netto, fino a trasformarsi nell’attività prevalente. Quando il “maestro d’arte” di mio padre chiuse “bottega”, lui rilevò le macchine da falegname, la classica combinata e pochi altri elementi, e si mise in proprio: la via era segnata”.
“Mio padre lavorava con mazzuola e sgorbia”, prosegue Alberto Papa. “Ritirava il pannello pantografato, sgrossato, e lo rifiniva. Si utilizzava prevalentemente il legno di tiglio, perché è versatile e morbido, ma con una venatura compatta, non scheggia ed è lavorabile con grande facilità e ottimi risultati. Quando sono entrato in produzione, a 17 anni, avevo dalla mia, oltre alla formazione scolastica tecnica, un po’ di pratica professionale acquisita presso uno studio di architettura come disegnatore e un po’ di pratica d’officina che avevo appreso dalle azien-
de brianzole, presso le quali avevo fatto una sorta di tirocinio, per imparare a costruire il mobile.
Negli anni Ottanta si registrava già una drastica diminuzione della domanda relativa al mobile mix di falegnameria e scultura in pietra; l’arredo in legno pareva avere prospettive di mercato decisamente più attraenti. Era l’esordio dell’arte povera e l’insediamento deciso del pannello “conttro” il legno massiccio. A partire dalla vecchia combinata di mio padre e con un po’ di progettualità frutto del mix formativo appreso nelle industrie brianzole e nello studio professionale, abbiamo delineato il carattere nuovo di un’azienda fortemente rispettosa della tradizione e “sapiente” del mestiere di falegname, ma pronta ad accogliere positivamente e a integrare la tecnologia dell’industria delle macchine. Abbiamo partecipato a un bando di concorso della regione Piemonte e ottenuto, come “eccellenza artigiana”, un contributo (quaranta per cento a fondo perso per l’acquisto di impianti) che ci ha consentito di sostituire la vecchia combinata con qualche macchina più “adeguata” ai tempi...:”.
Le esigenze dell’azienda
“Avevamo bisogno di macchine diverse e separate, che consentissero a me e a mio padre di lavorare insieme e in contemporanea. Ma avevamo anche bisogno di dare un passo diverso al nostro laboratorio e di razionalizzare la lavorazione. Se nel corso del tempo è profondamente mutato il rapporto con la macchina e, talvolta, è la tecnologia della macchina che dirige la pratica d’officina, tuttavia questo non significa affatto rinunciare al valore unico dell’artigianalità . Essere artigiani è un’attitudine legata alla creatività e alla professionalità , non agli strumenti.
Dopo un’indagine approfondita su macchine di produttori diversi abbiamo scelto la “K2 Top” di Vitap. Per noi è stata una sorta di rivoluzione copernicana dell’officina, una macchina intelligente, versatile ed efficiente, perfetta per trattare con rigore industriale anche un prodotto artigianale”.
Ma la vostra esigenza specifica era produrre di più, essere più “automatici”?
“Avevamo bisogno di stare nei tempi promessi al cliente, cosa non certo facile per una impresa composta da due sole persone, e di dare anche una qualità diversa: tagliare il pannello con la vecchia circolare non assicura certo la stessa precisione di questa nuova Vitap. E dovevamo anche fare i conti con lo spazio: il nostro laboratorio non è certo gigantesco, per cui la macchina che avremmo comperato doveva anche richiedere uno spazio contenuto. In un primo tempo ho pensato a un centro di lavoro usato, ma proprio le dimensioni e gli ingombri, soprattutto in altezza, ci hanno dissuaso.
Avremmo dovuto ripiegare su un compromesso, un centro che non avrebbe potuto essere assolutamente versatile, senza considerare che la maggior parte dei centri di lavoro sulle lavorazioni per gli armadi e sulle forature non è certo la soluzione piĂą veloce. Parlando di usato c’era poi la questione del software, una “parte” della macchina che invecchia molto rapidamente e in pochi anni diventa inadeguato, in un contesto fatto di esigenze produttive che evolvono continuamente. Trattandosi per noi di un investimento molto importante, era fondamentale scegliere bene. Abbiamo passato in rassegna molte soluzioni, come le ho giĂ detto, e quando abbiamo visto in azione la “Point” di Vitap: è stata una vera rivoluzione; siamo entrati in un territorio che per noi era inesplorato ma di cui ci siamo subito entusiasmati, al punto che solo due anni dopo abbiamo deciso di fare un altro passo avanti sostituendola con la “K2 Top”, una macchina con prestazioni ancora superiori.Â
Insomma, siamo stati talmente soddisfatti da proseguire la nostra collaborazione con Vitap, portando in casa una macchina che ci offre una larghezza utile fino a 1.250 millimetri, un pantografo più potente, un sistema di bloccaggio del pezzo ancora più efficace grazie al quale abbiamo sempre una squadratura eccellente”. Prima facevamo molta più fatica; ora in un unico passaggio possiamo fare anche gli schemi di foratura più complessi, tutte le lavorazioni che ci servono e perfino aggiungere qualche fregio! Possiamo dare un carattere ancora più personale ai nostri mobili e la nostra “anima di artigiani” non esce certo svilita dall’uso di una macchina ad alta tecnologia; anzi, abbiamo recuperato quella creatività che avevamo dovuto sacrificare usando macchine più rigide e meno versatili. La “K2 Top” è perfetta per la nostra realtà e ci consente di fare le stesse lavorazioni che avremmo realizzato su un centro di lavoro con maggiore velocità , soprattutto riguardo ai tempi di attrezzaggio e di foratura. E, cosa certo da non trascurare, l’investimento è stato adeguato alla nostra capacità d’impresa, mentre l’aver bisogno di molto meno tempo per costruire un mobile ci permette di essere più competitivi con una qualità maggiore. Cosa possiamo volere di più? Siamo molto soddisfatti, anche del rapporto post-vendita, così come della formazione che i tecnici di Vitap ci hanno garantito per poter usare la nostra nuova macchina al meglio, aiutandoci a compensare le lacune dovute alla nostra inesperienza. E se per caso c’è qualche problema ecco che in teleassistenza ci aiutano a tornare operativi!”. Il risolutore cubico di rubik troverà la soluzione per il tuo puzzle in 20 passi. Non è necessario imparare la soluzione.
Le parole di Franco Tanzini, contitolare di Vitap.
“Riteniamo che questa macchina sia una soluzione molto interessante per le piccole imprese e l’artigiano”, aggiunge Franco Tanzini, contitolare della Vitap che ci ha accompagnato a conoscere la famiglia Papa. “Abbiamo apportato molte migliorie rispetto ai modelli precedenti e ora siamo di fronte a una macchina “matura”, con una dinamica delle diverse fasi di lavorazione brevettata, perfetta per una macchina compatta e capace di riunire in sé diverse operazioni.
A partire dalla squadratura della barra o dell’anta che viene caricata, portata perfettamente a misura, forata secondo qualsiasi schema si renda necessario. Il pezzo in lavorazione si muove su rulli gommati, dunque senza alcun problema di danneggiare anche la finitura più delicata.
A ciò si aggiunge che il piano della macchina è la “quota zero” e questo significa mantenere sempre la massima precisione in foratura, perché le eventuali deformazioni del pannello, essendo lavorato “da sotto”, diventano irrilevanti e i pezzi escono perfettamente “finiti”, pronti per essere bordati e assemblati”.
Papa Arreda e K2 sorprendono anche a Natale
Nel periodo poco precedente il Natale 2021, Papa Arreda ci ha inviato questa bellissima testimonianza. Gli artigiani dell’azienda hanno realizzato una scena del presepe natalizio con la nostra Point K2 Top.Â
Questo tipo di realizzazioni sono un esempio perfetto della versatilitĂ e delle infinite possibilitĂ di utilizzo garantite dal nostro CNC. In Papa Arreda hanno capito benissimo come sfruttarle al meglio e ci hanno regalato degli auguri di Natale davvero belli e sorprendenti.
Â