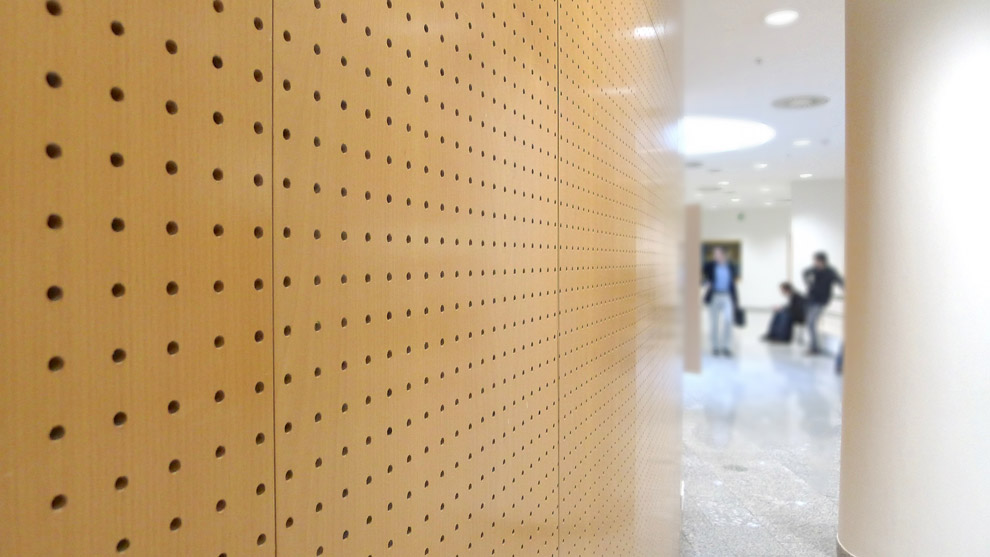
Sound absorbing panels and sound absorption: all you need to know
The concepts of sound-absorbing panels and sound absorption are becoming very familiar to those who have to combat noise pollution in interior spaces.
At Vitap we have developed some of the best machinery for making acoustic panels, and in this article we will explain these concepts in detail.
What are sound absorbing panels?
For sound-absorbing panels, particular coatings are indicated that have the aim of making an environment soundproofed. The sound-absorbing panels (not to be confused with the sound-insulating panels) have the function of limiting reverberation in confined spaces.
The reverb
To simplify the description, we can explain the acoustic phenomenon of reverberation, associating it with the simplest and most well-known concepts of rumble and echo, thus meaning it as the prolonged permanence of a sound.
In practice, in closed environments, the perceived overall noise is greater than the actual source that generated it since it is increased by the reflections produced by the walls, especially if they are made of smooth, compact materials (acoustically defined as reflective).
The amount of reverberation is usually expressed with the value of T60 which represents the time in seconds it takes for a sample of sound to reduce by 60 dB and is essentially the duration of the sound tail of sounds.
Texture and surfaces of the sound-absorbing panels
The panels which absorb sound are generally materials with a spongy consistency or in any case low density or compact materials (wood, metal, plastics, etc.), but with holes or cracks, and in this second case the true soundproofing function is provided by the associated soundproofing mat and left partially visible through the holes.
Panels which absorb sound can also have worked and colored surfaces and can be covered with fabric, combining the predominant function of "acoustic correction" with aesthetic and design value.
The surfaces that make up the panels are able to absorb most of the sound energy incident on them, reflecting only a minimal amount. The absorption coefficient is therefore the degree of sound absorption of a panel, it therefore varies depending on the type of material used, its stratification, its thickness, the chemical nature, the porosity and density, the rigidity and the shape of the components.
The panels can be fixed to the walls (fixed or removable) and / or placed on the ceiling in adhesion or lowered on cables in vertical baffle mode or in horizontal islands, as a variant they can also be arranged on mobile uprights and the Using an adequate number can greatly reduce the phenomenon of reverberation.
Wall panels can be installed continuously, creating an entire wall, or fixed in more or less groups and even individually.The fixing of the panels can be done with glues, making them fixed, or by the use of hooks and brackets, when you want to make them mobile.
WOODEN SOUND ABSORBING PANELS
The wooden sound absorbing panels give the rooms a prestigious character and an immediate feeling of warmth. The size and density of the holes determine the absorption performance of the panels. Sound absorbing wood panels generally have a panel coupled with PET polyester fiber which helps to increase the sound absorption power of false ceilings.
METAL SOUND ABSORBING PANELS
The perforated sound absorbing metal panels give the rooms a unique character and elegance, giving a strong hi-tech connotation. The size and density of the holes determine the absorption performance of the panels. Metal sound absorbing panels generally have a panel coupled to a PET polyester fiber which helps to increase the sound absorbing power of the panel.
Sound absorption
We now introduce the concept of sound absorption. Sound absorption is the ability of a material to absorb sound energy by turning it into heat, and it varies from material to material. The sound absorption of a material increases as the frequency of the sound wave increases, (Frequency is given by the number of identical events that repeat in a given unit of time and is measured in Hertz). A sound absorbing material should have both high "acoustic transparency", that is, high capacity for absorbing vibrating air (hence low resistance to flow) and good "sound dissipation". energy penetrated ”(ie high resistance to flow), therefore contradictory characteristics.
A porous body increases the dissipation of sound energy because its surface and the cavities that make it up are vibrated (thus effective at high frequencies), while an impermeable and compact body can be effective at low frequencies. it is flexible, damping and damping the sound waves that hit it. The absorption by porosity is due to the phenomenon of viscosity and the soundproofing capacity is influenced by the density and thickness of the body. Sound-absorbing materials for porosity are divided into fibrous materials (glass wool, rock wool, chipboard, cork, polyester fibers, gypsum, plasterboard, carpet, linoleum, curtains, natural and artificial fabrics of various types) and open cells (polyurethane foams, polyurethane foam, melamine foam).
Types of sound absorbent materials
FIBERGLASS
Fiberglass is an amorphous silicate, derived from glass, which is marketed in the form of rolls, mats and sound absorbing panels, has a great ability to incorporate air through a thick and soft structure and therefore to disperse the wave sound in heat. Certainly among the best soundproofing materials. Also excellent as a thermal insulator. A relatively inexpensive product that is very effective in reducing noise. Glass wools, like the rock wools described below, belong to the family of man-made vitreous fibers, also called (FAV) and are now seeing a gradual reduction in their use as noise absorbers for environments, because even incorporated into them. coating films, paints and fabrics, it is not possible to estimate the actual dispersion of fibers and micro-powders, in addition to containing traces of formaldehyde used in binders for fibers.
ROCKWOOL
Rockwool has characteristics similar to glass wool and derives from a special extraction process involving volcanic rock. It has flame retardant characteristics superior to those of glass wool. It comes in the form of panels and rolls.
CORK
Cork is certainly the best sound-absorbing material in nature. Preferable to glass and rock wool when ecological and sanitary needs are considered important, while having higher economic budgets than mineral wool. Available as carpet or sound absorbing panels.
WOOD PARTICLE BOARD
Wood particle board (or Chipboard) is made from the amalgam of wood fibers derived from leftover wood that are pressed and glued together to form rigid, strong panels. The result is a product with good soundproofing and sound insulation qualities.
Again, it is important to assess the amounts with which the formaldehyde-based binder is present in the compounds.
POLYESTER FIBER - PET (polyethylene terephthalate)
Polyester fiber is an excellent insulating and sound deadening material obtained from the recycling of PET plastics, which are reduced to fibers and bonded together without the use of glue or resin, but simply by heat (thermally bonded) and compacted in sheets of various thickness and density.
Laws and certifications related to sound absorption
Sound absorption capacity defines the acoustic characteristics of an object in the environment and is usually indicated by absorption coefficients measured at different frequencies. This means that a material has a different number of absorption coefficients depending on the frequencies. The degree of sound absorption is defined as reflection or absorption. To determine the absorption class of a product, a measurement is carried out according to the UNI EN ISO 354/2003 directive (Standard for "Measurement of sound absorption in a reverberant room") in the frequency ranges (third) from 100 Hz up to 5000 Hz over the reverb time. The result is represented as an absorption curve or table of values, which shows the absorption coefficients for each individual frequency used in the test. The sum of all absorptions and reflections of individual objects in the environment creates an acoustic image of the environment (reverberation) in our ear that makes us perceive the room as "reverberating" or "deaf". The so-called NRC ("Noise Reduction Coefficient") value was one of the first values with which an attempt was made to combine the information obtained from the absorption curve into a single value.
In accordance with the American standard ASTM C 423, it was calculated as the average of the absorption values of 250 Hz, 500 Hz, 1000 Hz and 2000 Hz with a deviation of 0.05.
The weighted sound absorption coefficient (αw) is established by the UNI EN ISO 11654 standard.
The standard specifies a method for converting the values of the sound absorption coefficient on the different frequencies, into a single evaluation index and therefore easier and more immediate to read even by non-experts, while consequently presenting a more restricted possibility of application in detailed acoustic analysis.
The UNI EN ISO 11654 standard is also adopted to classify soundproofing materials on absorption curves measured from A to E. Class A has the best absorption capacities while E has low capacities. The method of installation as well as the material properties affect the result the most. The classification system helps designers compare and select the appropriate absorption material for different purposes. The sound absorption properties of a material are expressed by the coefficient (alpha), as a function of frequency and varies from 0 to 1.00 (i.e. from total reflection to total absorption).
We hope this article was helpful to you. Discover all our machinery for the execution of acoustic panels or contact us at vitap@vitap.it for more information.