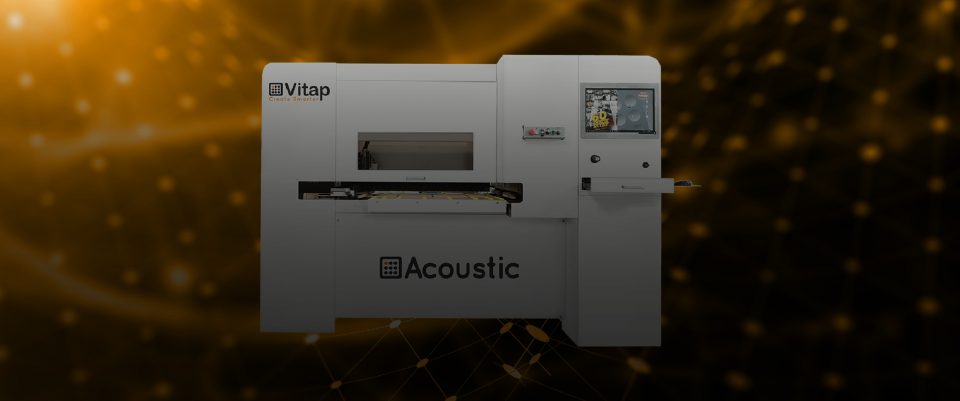
Make acoustic wood panels with a multi spindle drilling machine
Change your viewpoint: multi-drilling applied to sound isolation
Using multi spindle technology to produce acoustic and sound absorbing panels is a real innovation and guarantees incredible processing speed. With this in mind, Vitap has developed multi spindle drilling machines that make it possible to drill holes in wood acoustic panels much more quickly.
Point Acoustic is the machine that encloses this technological innovation in just 5 square metres and offers excellent performance in the production of acoustic panels in wood, aluminium and other materials. What exactly does multi spindle mean and why is it so advantageous? Basically, 55 spindles and quick chucks are applied to a monoblock drilling head: this means that, as it moves, Point Acoustic simultaneously drills a large number of holes, with wheelbase and depths that vary according to requirements. High productivity is therefore the greatest advantage of a multi spindle drilling machine but, thanks to Vitap technology, working faster does not mean working with less precision: the acoustic wood panels made by Point Acoustic are of excellent quality, machined with care and precision in every detail.
Meet Vitap Point Acoustic: born to fight noise pollution
Vitap is not only one of the leading companies in the production of woodworking machinery, but it is also an important research and development centre: within Vitap Lab we work every day to develop new machines, technologies and solutions.
Point Acoustic is the result of the scientific research we carry out with the aim of combating noise pollution: like other types of pollution, the noise one is also dangerous for our health, with harmful effects and physical disturbances in the short and long term. The attention on this issue is very high and for this reason in recent years there has been an increasing demand for acoustic panels. Today, this is a great business opportunity and Point Acoustic is the ideal machine to invest in the sector.
As a multi spindle drilling machine, it is able to ensure high production volumes and large profit margins, producing acoustic and sound absorbing panels of the highest quality.
Multi-boring facts: perform 55 holes in 4 seconds
Multi spindle boring machines therefore have a huge advantage over traditional acoustic panel making machines: they are much faster and ensure very high productivity.
Point Acoustic can drill in just 4 seconds 55 holes with a diameter ranging from 1 to 25 mm, simply by changing the size of the drills; thanks to the quick-change chucks with which it is equipped, this operation is immediate. For example, to complete a panel of 1 sqm, it will take less than 1 minute.
Point Acoustic is not only fast but also very precise. It is in fact a multi spindle drilling machine equipped with optimised drilling software, capable of performing precise and accurate machining down to the smallest detail. Like all CNC machines in the Point line, PC control is very simple and can be managed without problems by unskilled operators.
Add value to your drilling operations with customized heads
One of the distinguishing features of all Vitap's work is the continuous research for customer satisfaction: all the know-how and professionalism developed within Vitap Lab are used to seek solutions to the needs expressed by customers, in a process of continuous growth.
From these assumptions, the idea of giving added value to the Point Acoustic CNC machining centre was born, with the development of customized heads. This means that it is possible to carry out any type of machining, even the most specific and particular, thanks to special customized heads that are very easy to change.
Woodworking made easy for large and small companies
As the other woodworking machines in the Point line, Point Acoustic is the ideal solution for companies of all sizes.
It occupies little space, about 5 square meters, and does not require the intervention of highly qualified operators to be controlled: programming is easy and direct and there is a graphic editor to program the machining operations; the operator can set specific jobs and store them for possible future use, as well as you can optimize production based on the size of the panels to be processed.
It is therefore ideal for small companies which have limited budget but demand high quality, as well as for large companies that need large production volumes in a short time.