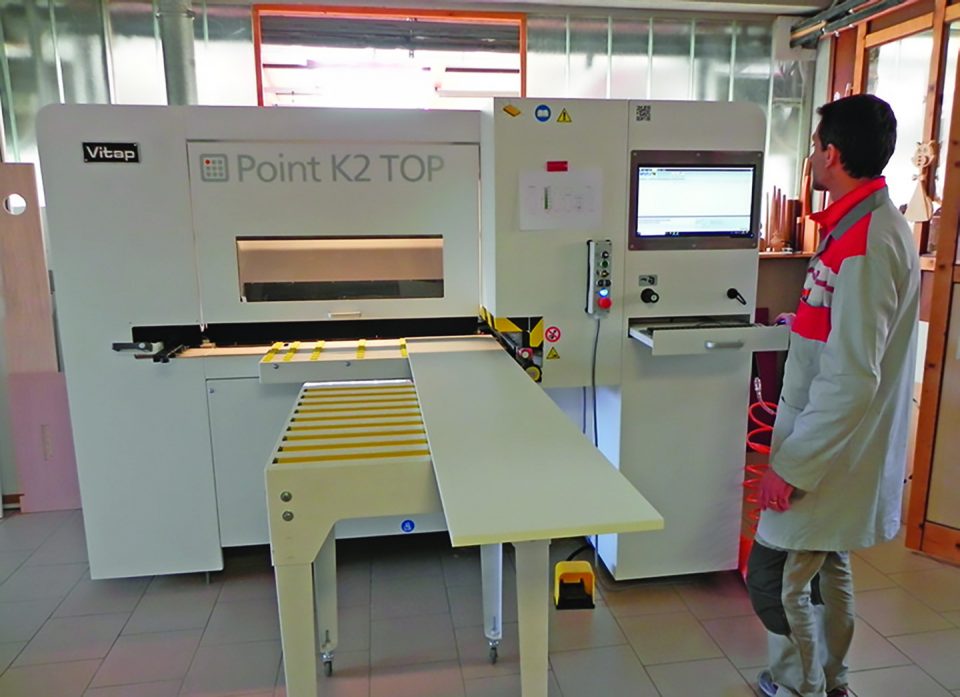
Free to invent: how Point K2 Top has responded to the basic needs of a carpentry
The Xylon magazine, in the month of April, gave voice to the Papa carpentry, a surprising micro reality that has made creative thinking its distinctive trait for three generations. They told how, introducing our CNC Point K2 Top working center in the company, was a real Copernican revolution for their reality.
Below is an extract from the article in the May-June issue of the magazine.
Alberto Papa and his father Enrico are the owners of PapaArreda, a family business located in Mergozzo, in the district of Verbano-Cusio-Ossola, which makes high-quality furniture. PapaArreda represents the artisan DNA and is characterized by what we might call the “somatic sign” of the Italian ingenuity. It has gone through 60 years of history and today reaffirms itself as an expression of an excellent carpentry, reinterpreting the processes and integrating the cutting-edge technology of the “K2 Top” panel processing machine
reinterpreting the processes it has chosen and positively integrating the cutting-edge technology of the Vitap "K2 Top" panel processing machine.
The company works in Lombardy, Piedmont and Switzerland. The privileged “marketing tools” are the word-of-mouth - and this says a lot about the high quality of the product and service - and the website, which describes the company effectively, leveraging its ability to “customize”.
A story, a family, a company
Alberto Papa, almost reluctantly, tells the fascinating history of its family, starting with his grandfather who was a sculptor, an artist profession, strongly rooted in the territorial reality: the Candoglia Quarries, in the municipality of Mergozzo, have given the marble to build the Milan Cathedral.
“My grandfather, Romeo Papa, began by working as a sculptor. In the fifties, he had attended the school of sculpture and carving and then he went to work for a sculptor affirmed in the area, Germano Tedesco, to learn the craft. Once the training was completed, grandfather Romeo chose to separate himself from its teacher and set up his own business of making frames for mirrors in baroque style. Turin was his reference market, where he was well known for his subcontracting business of marble elements for interior designers and furniture makers.
Grandfather also taught at the ex-Bellini school in Mergozzo, which trained mechanics and stonemasons. Initially, my father shared the choice of the grandfather and then focus on woodworking, an activity that belongs to the territorial tradition, although, today, local companies are more focused on fixtures. The specialization in furniture has decreased but we’ve been tied to the furniture, a real passion.”
From marble to wood
“Many carpenters were asking for marble friezes and processings to integrate their own furniture, cupboards and mirrors production. Contamination of skills and knowledge was spontaneous. With my entry into the company, the orientation towards carpentry work has become clear, until it becomes the main activity. When my father’s “master of art” closed his workshop, he took over the carpenter’s machines and set up his own business: the way was marked.
“My father worked with mallet and gouge - Alberto Papa continues - He withdrew the pantographed panel and finished it. Lime wood was mainly used, because it is versatile and soft, but with a compact grain, it doesn’t chip and can be worked with a great ease and excellent results. When I started working at the age of 17, I had a bit of professional practice acquired at an architecture studio as a draftsman and a bit of workshop practice learned from the companies in Brianza, where I had done a kind of internship, to learn how to build the furniture.
In the eighties, there was a drastic fall in demand for the furniture mix of carpentry and stone sculpture. Wood furniture seemed to have much more attractive market prospects. It was the beginning of the Poor Art and the decisive installation of the panel against solid wood.
Starting from my father’s old woodworking machine and with a bit of planning, the result of the training mix learned in the industries of Brianza and in the professional studio, we have outlined the new character of a company strongly respectful of tradition and expert in the carpentry profession, but ready to welcome positively the technology of the machinery industry. We have participated in a competition notice of Piedmont Region and obtained, as artisan excellence, a contribution (forty percent non-repayable for the purchase of equipment) that has allowed us to replace the old woodworking machine with some machinery more appropriate to the times.”
The company needs
“We needed different, separate machines that would allow my father and I to work together and at the same time. But we also needed to change tack in our laboratory and rationalise the process. If over time the relationship with the machine has deeply changed and, sometimes, it is the technology of the machine that directs the laboratory work, however, this does not mean giving up the unique value of craftsmanship.
Being an artisan is an attitude linked to creativity and professionalism, not to instruments. After a thorough investigation of machines from different manufacturers, we chose Vitap's "K2 Top". For us it was a sort of workshop Copernican revolution, an intelligent, versatile and efficient machine, perfect for treating a handmade product with industrial rigour.
But was your specific need to produce more, to be more "automatic"?
“We needed to meet the deadlines promised to the client, which was not easy for a company made up of just two people, and also to give a different quality: cutting the panel with the old instruments certainly does not ensure the same accuracy as the new Vitap machine. And we also had to deal with space: our laboratory is not gigantic, so the machine we would have bought also had to require a small space. At first I thought about a second-hand machining centre but precisely the dimensions and the encumbrance, especially in terms of height, dissuaded us. We would have had to turn to a compromise, a centre that could not have been absolutely versatile, without considering that most of the machining centres isn’t certainly the quickest solution for machining for wardrobes and perforations. About second-hand, there was even the problem of software, a "part" of the machine that ages very quickly and in a few years becomes inadequate, especially in a context where production needs are constantly evolving. This is a very important investment for us, so it was essential to choose well.
We have reviewed many solutions until we saw in action the Vitap “Point” machine: it was a real revolution. We entered a territory that for us was unexplored but we were immediately excited, to the point that only two years later we have decided to take another step forward by replacing it with the “K2 Top”, a machine with even greater performance. In short, we were so satisfied that we went ahead our collaboration with Vitap, by bringing home a machine that offers a working area of 1250 mm, a more powerful pantograph, a piece locking system even more effective thanks to which we always have an excellent squaring.” We used to have a lot more trouble. Now in a single step we can do even the most complex drilling patterns, all the processings we need and even add some friezes! We can give an even more personal character to our furniture and our “soul of craftsmen” does not come out debased by the use of a high technology machine; on the contrary, we have recovered the creativity that we had to sacrifice by using more rigid and less versatile machines.
The "K2 Top" is perfect for our reality and allows us to do the same work that we would have done with other machining centre with higher speed, especially regarding setup and drilling times. Then, do not neglect that the investment has been adequate to our business capacity, while having need much less time to build a piece of furniture allows us to be more competitive with higher quality. What more can we want? We are very satisfied, even with the after-sales relationship, as well as the training that the Vitap technicians have given us to use our new machine at best, helping us to compensate for the shortcomings due to our inexperience. And, if there is a problem, here is the tele-assistance helps us to back up and running!".
The words of Franco Tanzini, co-owner of Vitap.
"We believe that this machine is a very interesting solution for small businesses and craftsmen", adds Franco Tanzini, co-owner of Vitap, who has accompanied us to meet the Papa family.
"We have made many improvements compared to the previous models and now we are dealing with a "mature" machine, with a patented dynamics of the different processing phases, perfect for a compact machine capable of doing together different operations.
Starting from the squaring of the bar or the door that is loaded, perfectly sized, drilled according to any scheme that may be necessary.
The workpiece moves on rubber rollers, so there is no problem in damaging even the most delicate finish.
In addition, the machine table is the "zero quota", which means that the maximum precision in drilling is always maintained, because any deformations of the panel, being machined “from below”, become irrelevant and the pieces come out perfectly “finished”, ready to be edged and assembled.
Papa Arreda and K2 surprise even at Christmas
In the period shortly before Christmas 2021, Papa Arreda sent us this beautiful testimony. The company's artisans created a Christmas nativity scene with our Point K2 Top.These kinds of creations are a perfect example of the versatility and infinite possibilities of use guaranteed by our CNC. In Papa Arreda they understood very well how to make the most of them and gave us really beautiful and surprising Christmas greetings.